Will Sodium replace Lithium in Batteries? It might, but it won't
Technology
August 19. 2024
3 min.
expert article
2024 is to be the year of the sodium-ion battery (SIB), or at least that's what they say. Compared to Li-ion, SIBs offer similar power delivery characteristics at a lower cost. Are they the next big thing?
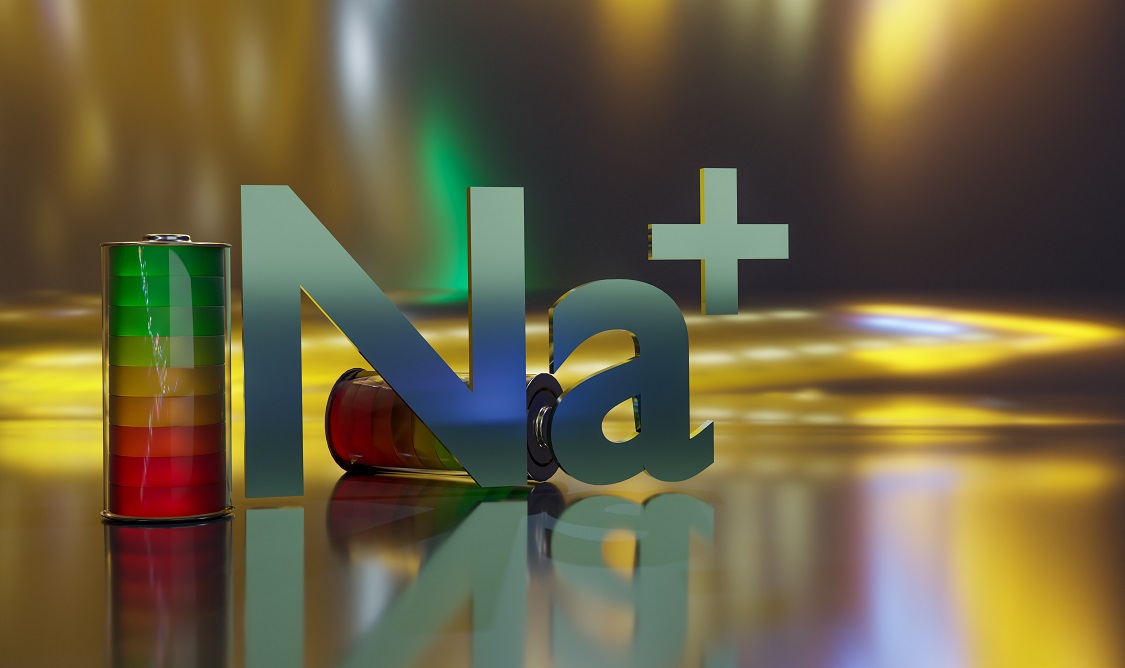
To say that SIBs are fairly comparable to lithium-ion batteries, or LIBs, is almost an understatement. For starters, both chemistries are based on a very similar working principle, or at least most of SIB varieties. Only instead of lithium, SIBs use sodium ions (Na+) as charge carriers. Both elements being alkali metals, their shared electron configuration results in very similar chemical properties, especially a high degree of reactivity as their valence shell contains only one loosely held electron.
Important differences between the two include the fact that while lithium deposits are rather limited, sodium is actually the sixth most abundant element in the Earth's crust. Because it’s so keen on bonding with other elements, sodium does not occur as a free metal in nature, but it is found in many minerals including some very soluble. Such as sodium chloride (NaCl), widely known as common salt, which is our main source of sodium. From NaCl, pure sodium is being prepared by means of electrolysis in an apparatus called Downs cell.
A tale of two chemistries
Having whole oceans of saltwater at our disposal, while lithium is geographically very unevenly distributed and its extraction process environmentally problematic, led both researchers as well as the industry to increasingly focus on SIBs in the past few years. However, the history of SIBs goes back three or four decades and is quite intertwined with the story of Li-ion batteries. The development of both chemistries began in the 1970s, and in a way, they initially competed with each other.
In the decade to follow, a handful of US and Japanese companies introduced first working SIB cells. With a sodium-lead alloy on the anode and sodium cobalt oxide on the cathode, these cells had a lifespan of over 300 cycles. This seemed quite promising at this early stage of the development, but what was less impressive was their discharge voltage of below 3.0 V in comparison to the respective performance of lithium-ion.
But more importantly, it became soon obvious that SIBs would never match the energy density of LIBs. This is because Na+ are 25 percent larger than Li ions which affects their transport properties and interphase formation. Sodium is also roughly three times heavier than lithium, and has a higher standard electrode potential, i.e. a lower ability to be oxidized. A sodium-based chemistry will therefore always fall short in terms of energy density. Current SIB's specific energy ranges between 100-200 Wh/kg which is roughly a fourth less than most Li-ion chemistries.
Li-ion also took a lead in terms of commercial maturity, as the chemistry's major problems including structural degradation and flammability have been resolved by the mid-1980s. SIBs, however, were plagued with serious issues up until the 2010s. Researchers particularly struggled to find a suitable anode composition. Graphite, while the perfect device for lithium storage, turned out to intercalate only a negligible amount of sodium ions. Recently, grinding graphite into nano-scale flakes has shown a major increase in Na+ adsorption and intercalation capabilities, but twenty or thirty years ago, crystalline carbon seemed a dead end.
Making it work
Researchers thus began exploring a wide range of different anode compositions, including coating the electrode with a nickel antimony alloy, molybdenum disulfide, or titanium sulfide, but the most promising turned out to be carbon still. More precisely hard carbon, a low-density form of the element similar to charcoal which, as anode material in SIBs, offers high-enough conductivity as well as a decent specific capacity and other characteristics. On the other hand, unlike graphite, hard carbon undergoes greater structural changes during cycling which may limit the battery's lifespan.
Furthermore, hard carbon for SIBs is mostly derived from organic sources such as cellulose or resin by means of pyrolysis, often requiring post-processing by microwaves. Thus, there are doubts about sufficient commercial scalability of current hard carbon production if SIBs really make a breakthrough. However, alternatives better adaptable for large-scale production are being explored. Particularly spark plasma sintering which, in addition, provides hard carbon with higher conductance and lower oxygen contents.
Different materials have been studied for the cathode too, primarily multiphase layered transition-metal oxides (LTMO) with their chemical formula typically being NaxMO2 where M stands for elements such as Ni, Mn, Fe, Co, or Cu. Most of these metals can be prepared very cost-effectively, and LTMO-based SIB cells also offer a respectable capacity. On the other hand, these materials do not improve on the inherent weaknesses of SIBs, particularly slower intercalation kinetics, and may exhibit a less sufficient integrity.
Some of these characteristics can be improved by elemental doping, i.e. furnishing the cathode material with electrochemically inactive Mg, Li, Zn, and Al, or by coating the electrode with aluminium oxide. Another way to improve the intercalation in LTMO cathodes is altering the morphology of the electrode as such, utilizing designs based on microsheets, nanofibers, or a hierarchical columnar structure.
But there are other perspective materials to experiment with as well, including a range of sodium-based polyanionic compounds. Such cathodes provide favorable cycling characteristics and desirable operational voltage, but at the expense of a lower energy density of the cell due to the polyanion-type materials' poor conductivity. Similarly to LTMO cathodes, possible remedies include surface modifications, elemental doping or optimization of morphology.
Cathodic materials based on Prussian blue (PB), or rather its analogues (PBA), are being extensively researched as well. Because the large Na+ have their difficulties passing through the PB cavities, PBAs were developed where the PB's Fe centers were replaced by other metals such as Mn, Co, Ni, or Zn. The advantages of PBA cathodes include structural stability, low cost, and also environmental friendliness, the major drawback being a lower energy density. In other words, the quest for the perfect SIB cathode is by far not over yet, as currently almost twenty different cathode materials are being explored.
Furthermore, each variety of SIB, of course, requires an appropriate electrolyte composition. Most SIB electrolytes make use of a sodium salt dissolved in an organic solvent and may also come with significant disadvantages. Sodium perchlorate, for instance, while not combustible in itself, is capable of accelerating the burning of combustible materials to the point of an explosion. Meanwhile sodium hexafluorophosphate is highly susceptible to reacting with water to form the toxic hydrogen fluoride.
No revolution ahead
All in all, the chemistry has not quite yet reached market maturity, but it's certainly nearing the finishing line in this regard. In the last year or two, major investments including government funding were poured into SIB development. Especially in Europe, as the continent strives to reduce its dependence on lithium imports, but also in China and, with a little delay, in the US, too. In fact, most SIBs use the same production processes as LIBs, which is a very strong argument for the chemistry. Retrofitting a LIB plant to produce SIBs is estimated to require only 10 percent additional capital expenditure. And once gigawatt-hours production capacities are reached, SIBs could be up to 30 percent cheaper than LIBs.
In practical use, SIBs offer fast charging ability, reasonable temperature stability and safety against overheating or thermal runaway. And last but not least, they are less toxic than other commonly used battery chemistries. The lack of an established industrial supply chain will surely be overcome quickly, but the electrochemical limitations of the technology may not, including the lower energy density or shorter lifespan of SIBs.
So, they will most likely not turn the battery market upside down, nor will they fully replace LIBs. Instead, at least in the foreseeable future, SIBs may very well complement LIBs and also lithium-sulfur or other upcoming chemistries. Maybe while premium products will use LIBs, Li-S or whatever else, SIBs will be the chemistry of choice for less expensive cars and electronics, not to mention their suitability for industrial-grade storage.
Sources:
Yun Gao, Hang Zhang, Jian Peng, Lin Li, Yao Xiao, Li Li, Yang Liu, Yun Qiao, Shu-Lei Chou. 2024. A 30-year Overview of Sodium-ion Batteries. Carbon Energy, Volume 6, Issue 6. Available online at onlinelibrary.wiley.com
Yu Tian, Hua Yang, Yujie Zeng, Yanyuan Qi, Wenxuan Wang, Huaican Chen, Wen Yin, Yubin Ke, Zelang Jian, Wang Hay Kan, Wen Chen. 2023. Design of High-Performance Defective Graphite-Type Anodes for Sodium-Ion Batteries. ACS Applied Energy Materials, Volume 6, Issue 7. DOI: 10.1021/acsaem.2c04140
Gupta P, Pushpakanth S, Haider A, Basu S. 2022. Understanding the Design of Cathode Materials for Na-Ion Batteries. ACS Omega, Volume 7, Issue 7. Available online at pubs.acs.org
Mingyi He, Shaomin Liu, Jiating Wu, Jinglin Zhu. 2024. Review of Cathode Materials for Sodium-ion Batteries. Progress in Solid State Chemistry, Volume 74. DOI: 10.1016/j.progsolidstchem.2024.100452
Related articles
Lithium-Sulfur: On the Brink of a Revolution
February 22. 2024
3 min.
expert article
VíceLithium or Nickel – to whom does the Future belong?
February 22. 2023
2 min.
Více